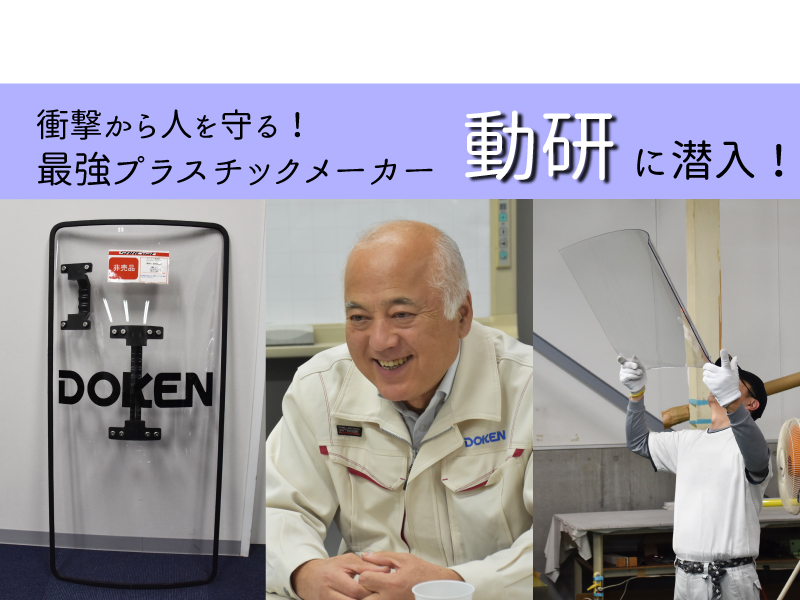
誰もが一度は見たことがあるだろう。
布に擦れて傷だらけになったり、太陽にあたって黄色くなったりした、劣化した『プラスチック』。
右のプラスチックは、太陽光にあたり劣化が進んでいる
私たちの身の回りには、プラスチックが溢れている。
例えば、ヘルメットのシールド。
この透明なプラスチック部分が、冒頭のように劣化してしまったらどうなるだろう。
※写真はイメージ
前が見えなくなり、きっと、使い物にならない。
こんな問題を解決する“モノづくり”の会社が、新城市にある。
株式会社 動研 だ。
動研は、「ポリカーボネート」という種類のプラスチック成型と、そこに「シリコンハードコート」という表面処理を行うことで、頑丈で傷つきにくいプラスチックを造るメーカーである。
今回はこの動研に潜入し、最強プラスチックの秘密を探ってきた。
動研の作る最強プラスチック
ポリカーボネートとは?
冒頭で紹介したヘルメットのシールドや、バイクのスクリーン、防弾盾などは、「ポリカーボネート」という種類のプラスチックが使われている。
ポリカーボネートは、ガラスの半分の重量で200倍もの衝撃に耐えられると言われる、軽さと耐衝撃性に特徴のあるプラスチックだ。
また、ガラスに引けを取らないレベルで透明性にも優れており、様々な場面で利用されている。
動研は、この「ポリカーボネート」の成形を得意とするメーカーなのだ。
ポリカーボネート成形
動研では、2つの方法でポリカーボネートの成形を行う。
1つ目が、「プレス成形」だ。
ポリカーボネートの板をおおよその形にカットしたのち、木製の型でプレスすることで目的の形にする。
動研の工場に入ると、通路脇にはズラリと木製の型が並ぶ。
残念ながら企業秘密でお見せ出来ないが、誰もが知る大手メーカー製品の型も数多い。
動研では稼働中のものだけで1,700種の製品がある
熱して柔らかくしたポリカーボネート板をプレス機にかけ、じっくりとプレスすることで成形する。
その後再度不要な部分をカットし、成形工程は完成だ。
2つ目の成形方法は、「射出成形」だ。
ポリカーボネートの粒を溶かし液体にしたのち、金型に液体を流し込み、冷やし固めることで目的の形にする。
(左上)射出成形機/画像:MITSUBISHIemシリーズ
(右下)射出成型の仕組み/画像:射出成形とは
射出成形は、素材を一度溶かしてから金型に流し込むという方法なので、プレス成形では作るのに時間のかかる複雑な形状の製品を短時間で作ることができる。
一方で、プレス成型は比較的安価な木製の型を使用するが、射出成型では重さ3~10トンの大型で非常に高価な金型を必要とする。
このように2つの成形方法にはそれぞれ得意不得意があるため、取引先のニーズに沿った成形方法を提案している。
射出成形では複雑な形状の製品成形も短時間で可能
他社にマネできないポリカーボネートの成形技術
一般的に、ポリカーボネートの成形は他の樹脂に比べて難しいと言われている。
歪(ひず)みが出来たり、線が入ってしまったりするため、ポリカーボネート成形には高い技術力を必要とする。
「ただ曲げるだけに見えるが、本当はちょっと難しい。」
謙虚気味にそう語るのは、動研の創業者であり、現在も社長を務める安藤社長だ。
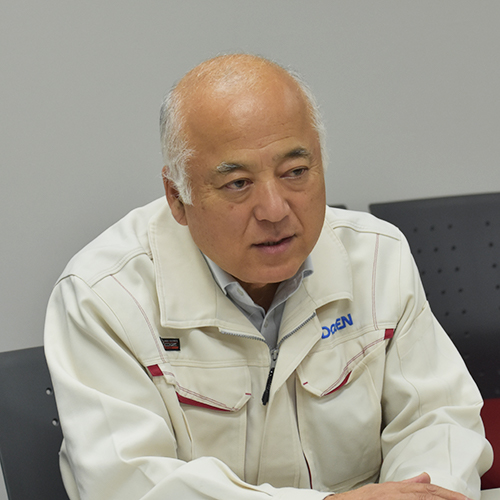
株式会社 動研
代表取締役社長
生粋のエンジニアである動研の創業者
安藤社長
「かつてポリカーボネート製品はとんでもなく高価なものでした。それは、職人が手作業で時間をかけて曲げ、ノコギリで切って作っていたからです。
頑丈で透明度の高いポリカーボネートに将来性を感じた私は、『機械化して安価なポリカーボネート製品を作ろう』と考えたのですが、始めは全く上手くいきませんでした。どうしても思い通りにならなかったのです。」
作り始めは100%不良品。満足いく製品が作れるまで、1年半かかったという。
安藤社長
「初めての受注は関西のメーカーからの量産の依頼だったのですが、線が入ったり表面にブツブツが出来たり、とにかくキレイに作れない。
納期ギリギリまでかかったため、最後は車で輸送する時間が無くなり、社員みんなで大きな製品を抱えて新幹線で運びました。」
新幹線で運んだ逸話は、社内で伝説となっているそうだ
それほど加工が難しいポリカーボネート成形。
この1件を通じて習得された動研の技術は、日本全国から求められるようになった。
いつのまにか『ポリカーボネートの加工に困ったら豊橋(動研の旧工場)へ行け』が合言葉になるほど、様々な業種のメーカーから頼りにされている。
動研を世界に導く、もう一つの技術
ポリカーボネートの弱点を補う『ハードコート』処理
頑丈なポリカーボネートにも、布でこすると擦り傷が付きやすかったり、太陽にあたると黄色くなってしまったりするという弱点がある。
これを防ぐのが、動研がもう一つ得意とする「ハードコート処理」という技術だ。
動研ブランド「SARCoat(サーコート)」
動研は、自社ブランド「SARCoat(サーコート)」というシリコン系ハードコート処理剤を使い、ポリカーボネートの弱点を補う。
まずは前処理として、出来上がったポリカーボネート製品の表面につくゴミやホコリを取り除き、傷などが無いか徹底的にチェックする。
ハードコート処理の前に、表面を徹底的にキレイにする
前処理を終えたポリカーボネート製品は、動研独自の技術が詰まった全自動のハードコート処理加工設備により、ムラなく「SARCoat(サーコート)」液に浸けられ、表面処理が施される。
ハードコートは全自動制御で施される
この表面処理により、ポリカーボネート製品は頑丈さだけでなく、耐擦傷性・耐候性・耐薬品性・耐溶剤性を手に入れるのだ。
コーディング処理されたシールド。耐擦傷性、耐候性等の機能に加えて、ゆがみのない均一なコート膜が要求される
安藤社長
「ポリカーボネートの成型加工から、その弱点を補うシリコンハードコート処理までを一つの工場で出来る一貫工場は寡占状態です。つまり動研は、日本一、世界一を狙える会社だと思っています。」
安藤社長がこう発言する裏には、自動車業界のトレンドがある。
もう、遠い夢ではない
現在の自動車業界のトレンドは、なんといっても「EV(電気自動車)化」と「自動運転化」であろう。
EV車普及に向けた大きな課題のひとつに、「航続可能距離」の問題が存在する。
エンジン車と比べ、電気自動車が1回の充電で走ることのできる距離はまだまだ短い。
それを解決する方法として「車両の軽量化」が注目されている。
安藤社長
「ポリカーボネートにシリコンハードコート処理を施すことで、頑丈で傷つきにくく、太陽光にあたっても劣化しにくいプラスチックを作ることができます。
現在は車のウィンドウにはガラスが使われていますが、これをポリカーボネートに置き換えることで車両の軽量化が実現できます。
また、EV化や自動運転化に伴い、自動車のデザイン性はどんどん新しいものになっていきます。
そういった意味でも、ポリカーボネートであればデザインの自由度はとても高くなるでしょう。」
ガラスには出来ない、自由なデザインを可能とするポリカーボネート
他社にマネできない技術力で、最強プラスチックを作る株式会社 動研。
近い未来、
日本中、いや世界中を、動研のポリカーボネートを載せた自動車が走り回る日が来るかもしれない。
そんな株式会社 動研では、現在一緒に働く仲間を募集中!!
≪正社員募集ページ≫
【会社概要】
株式会社 動研
代表取締役社長:安藤 英世
愛知県新城市一鍬田道目記1-21 新城南部企業団地
0536-24-5100
HP:http://www.doken.biz/
**********************************************
SNSをフォローして、
TASUKIの最新情報をチェック!
**********************************************
【Facebook】
【Twitter】
Follow @tasuki10484
Tweets by tasuki10484
■□■東三河の求人サイト**TASUKI**■□■
こんな仕事が東三河に!?という仕事が多数掲載!
「地元で仕事を探そう」と思ったら、まずはTASUKIをチェック!
【地域】 豊橋 豊川 蒲郡 新城 田原 東三河
【雇用形態】 正社員 パート アルバイト 新卒 転職
【職種】 製造 技術 開発 販売 営業 事務 IT 軽作業